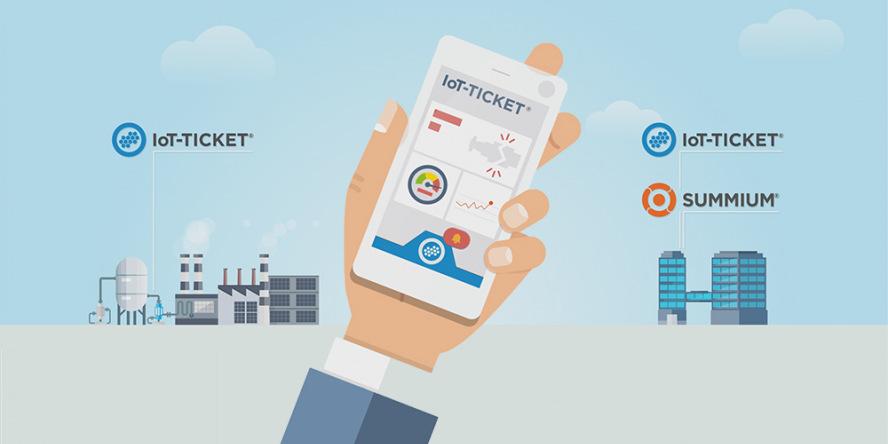
From scheduled maintenance towards need-based maintenance
- iot-ticket
- CPQ
- sales configurator
- services
Nowadays a lot of different usage data is gathered from industrial products, including amount of usage, status and location information of the products as well as wearing of components. Often this data is used for preventing product failures or offering value-added services to customers. A real-time product life-cycle data can also be utilized in sales by combining Internet of Things (IoT) solutions with CPQ sales tools.
During the past couple of years Wapice has participated in D4Value research project funded by Business Finland. In this project we have researched what kind services industrial companies could offer to their customers utilizing product life-cycle data. By combining Wapice’s products, IoT-Ticket and Summium CPQ, completely new service possibilities open up to industrial companies. Here is one example:
An industrial company has delivered a product to a customer, and the product is being monitored in real-time with IoT-Ticket. When IoT-Ticket notices a deviation or an unwanted trend, it sends the information to the supplier’s Summium CPQ, which then analyses the deviation and generates a solution proposal.
This proposal may consist of replacing of an entire product, changing its components or performing a maintenance procedure. With the information received from IoT-Ticket, a sales manager or a service manager can then create a maintenance quote and send it to the customer. After the customer approval, the maintenance can be performed.
Wapice has published a new concept video which illustrates how need-based maintenance could be accomplished.
This way companies can move from scheduled maintenance towards need-based or usage-based maintenance. Existing technologies already make this possible. This combination enables companies to offer new kinds of value-added and process optimization services as well as cross-selling and upselling possibilities to their customers.
For example, products that are in the end of their life-cycle, can be identified and replaced before they fail. In process industry so called bottleneck products or process phases can be replaced in order to increase process capacity. These are just few examples, and many more could be recited.