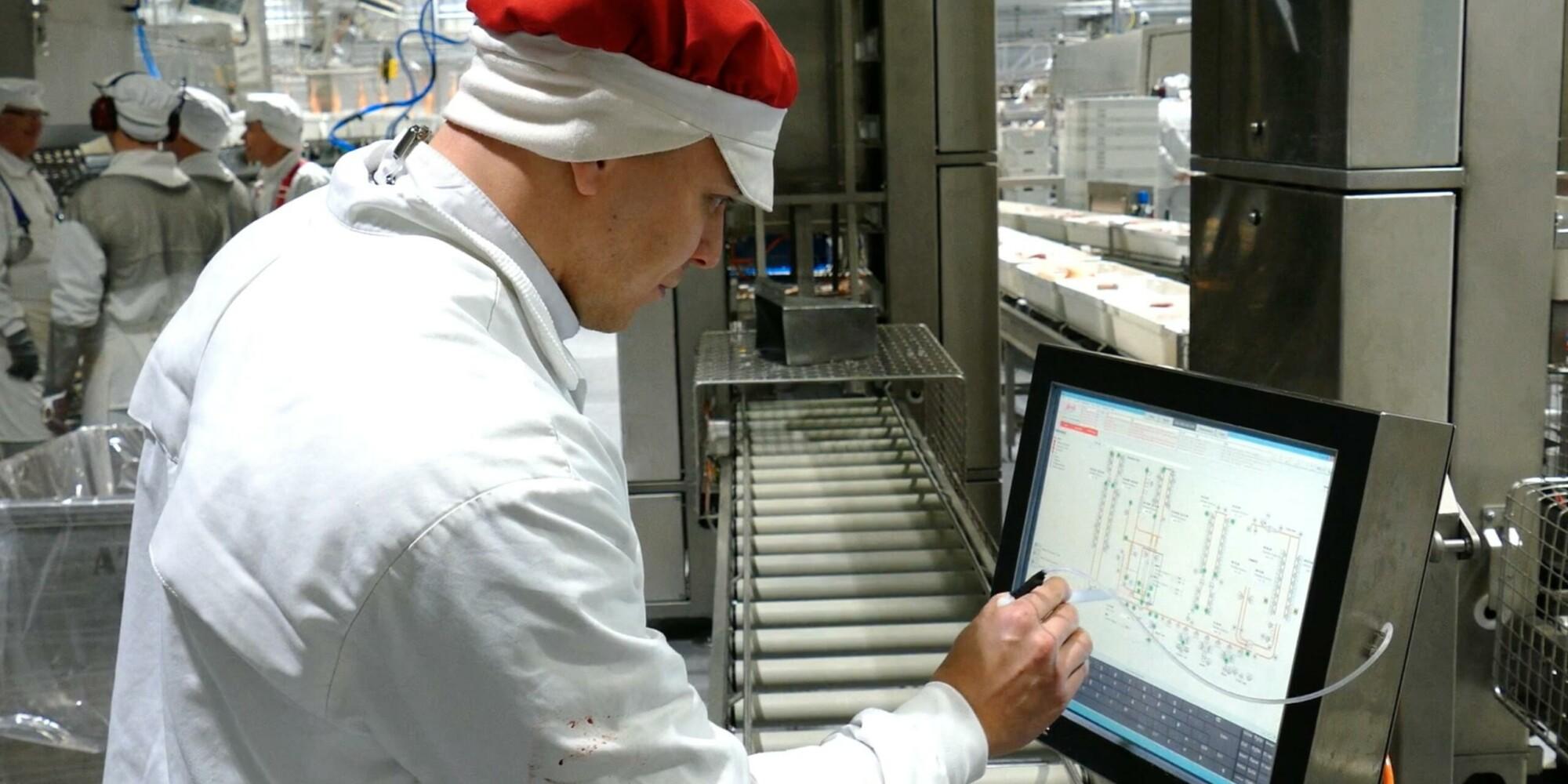
Atria uses Wapice’s data collection solution to enhance knowledge-based management
Wapice and Atria joined forces to build a Smart Factory solution, which automates the collection of production data. The project involved the creation of a data model for data collection and a configurable data collection service. Both have been designed from the outset to be scalable for enterprise-wide use.
Challenge
With a large number of players and industrial processes, it is important that data is collected and processed in the same way across the organisation.
“We didn’t have a solution for how to collect data from the process equipment so that it could be combined with the other data we were generating. There was no ‘off the shelf’ solution,” says Pasi Marttila, System Manager at Atria, about the project’s background.
In a company of this size, there are plenty of innovative, talented people who can solve any problem. From an IT perspective, however, the challenge is that soon there may be a multitude of different systems to maintain.
“That is why we needed an organisation-wide model for data collection,” says Marttila, describing the challenge of a large organisation.
Atria has a long history of knowledge-based management, partly due to industry legislation and the ‘traceability of origin’.
“Our data and processes have supported knowledge-based management long before the current passion for data. Our meat packages indicate very clearly where the meat comes from, and this has been the case for a very long time.”
Solution
Atria aimed for a tailor-made solution from the start.
We couldn’t find an off-the-shelf product that would meet our needs. On the other hand, we also did not want to commit ourselves to a single supplier ecosystem. So we set out to develop our own solution together with Wapice.
After the initial stages of defining needs, the work started to progress rapidly.
“Atria ordered a data collection and reporting solution from Wapice to support its Smart Factory concept for digitalisation, which focuses on intelligent monitoring, tracking and control of the factory and its production lines. The solution created in the project is based on a generic data model and a configurable and scalable data collection service that can be deployed in a straightforward manner, one department and production line at a time,” says Juha Viskari, Lic.Sc. (Tech.), Project Manager at Wapice.
“What is typical of production equipment is that each piece of equipment can process production and equipment status data in many ways and independently of each other.”
The inconsistency of the raw data from the equipment is a challenge for systematic data collection and reporting. The data model of the solution enables consistent data storage and processing as part of Atria’s other production reporting.
“Departmental reporting is also possible. The reporting provided serves production, maintenance and management. In the first phase, event and fault reporting and real-time access were implemented for production needs at the Kauhajoki factory,” says Wapice’s Juha Viskari.
“Technically, the solution is implemented by capturing production data from MQTT-compliant data sources via RabbitMQ buffering to a Windows Server-based data collection service that harmonises the data. The processed data is stored in a SQL Server database, from where it is available for Power BI and SSRS reporting,” says Viskari.
Results
The data model and data collection system developed in the project has already been piloted in Atria’s Kauhajoki unit.
This project has provided us with data models for incorporating data from the production process in the same system, further improving traceability. Naturally, this also reduces manual maintenance work,” says Marttila.
“Now we have a model for how to collect data from equipment so that it can be combined with other data. This is something we can leverage across the Group. The solution also allows production data to be brought into the same system, resulting in easier traceability. We piloted the practical use of the model in the Kauhajoki unit and the experience was good. At Group level, however, the biggest benefit has already been achieved through the data model developed in the project,” says Atria’s Pasi Marttila.
Cooperation
Marttila praises the cooperation with Wapice.
“The project ran according to expectations and the quality of work was excellent. The project was a success all round. The data model is now ready, and the next step is to put it into practice. However, we do not do this for the fun of experimentation; there must always be a business rationale,” Atria’s Pasi Marttila sums up.
Marttila sees a lot of opportunities for further exploitation of the system. “Process equipment collects data such as temperatures, baking times, cooling times and fault codes, continuously generating information for a real-time view. Now we can collect data on events, electricity consumption and so on,” Marttila says.
The Atria Group is one of Northern Europe’s leading food companies. The renewal and growth of the company, founded in 1903, are based on excellent commercial skills and an efficient, responsible corporate culture. In 2023, the company had a turnover of around EUR 1.8 billion and employed around 3,900 meat and food industry professionals in Finland, Sweden, Denmark and Estonia. Atria’s core product, Good Food, makes people feel better and delivers sustainable value to all its stakeholders. Atria Plc’s shares have been listed on Nasdaq Helsinki Oy since 1991.
Additional Information
Wapice Oy
Juha Viskari
Atria Oyj